Metal vs. Plastic Belts
Are you considering using plastic belts on your spirals, either to replace metal belts on existing units or to design new spirals with plastic?
Are you considering using plastic belts on your spirals, either to replace metal belts on existing units or to design new spirals with plastic?
With new plastic materials, solid engineering and application support, and strong belt warranties, you should look at plastic spiral belts in your next application.
If you have an application coming up for a spiral, let us take a look at it. We will give you a specific analysis of the belts you are considering for a specific product and environment, and we can help you choose the best belt for the application.
The use of metal belts on spirals is well documented for their abilities and limitations.
Plastic spiral belts have less history, although in straight-running applications, plastic belts have proven to outwear metal by a 3:1 factor. Time will tell if this also applies to spiral radius belts.
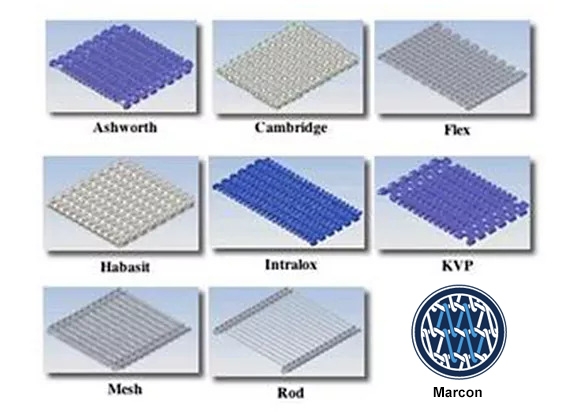
A Brief Metal Versus Plastic Belts for Freezers Advanced Spiral, Tunnel Freezer Manufacturer — Spiral Freezers, IQF Freezer Manufacturer, Tunnel Freezers
Belting Manufacturers
The various types and styles of belting are available for spirals. Unlike straight-running conveyors, spirals can only use belts that can make a radius turn, which limits the types and styles that can be used on these systems.
The manufacturer lists belts.
- Marcon
- Ashworth
- Cambridge
- Flex
- Habasit
- Intralox
- KVP
- Mesh
Rod, The final decision about selecting a belt should be made between you, the spiral manufacturer, and the belt manufacturer. We also list a brief description of the belt's main characteristics for your initial evaluation and a general comparison between plastic and metal belts.
If there are belt manufacturers that would like to be considered for listing and have not been included, please feel free to contact us. We have listed 95% of all spiral belts currently used on low-tension spirals. We have not listed belts of special proprietary design that can only be used on a single type of spiral.
Strength:
Advantage: Plastic
Currently, the most robust plastic belts are 550 lbs of plastic and 500 lbs of metal. Not all plastic or metal styles carry this rating. As strength is not the most critical factor (it is the radius weight rating), plastic belts have an advantage over metal.
Weight:
Advantage: Plastic
Plastic belts weigh:
1" pitch: 1.1 lbs/sq. Ft.
1 1/2” pitch: 1.7 lbs/sq. Ft.
2" pitch: 2.76 lbs/sq. Ft.
Metal belts weigh:
Rod type: 1.85 lbs/sq. Ft.
Flex type: 3.2 lbs/sq. Ft.
Mesh Overlay type: 3.05 lbs/sq.ft.
In weights, the lighter, the better (assuming no strength loss). Plastics have it over metal.
Fatigue:
Advantage: Plastic
Plastic belts are not subject to work hardening as metal belts are, so the continuous cycling of the belt through the spiral does not have the same detrimental effect on the plastic as it does on metal.
Collapse:
Advantage: Metal
Metal belts (various styles) have collapse factors of:
2.2 to 1
1.7 to 1
1.5 to 1
1.1 to 1
Current Plastic belts have collapse factors of:
2.2 to 1
1.7 to 1
A smaller collapse factor in a belt gives you a smaller footprint (smaller cage diameter possibilities), so the metal has it over plastic (today).
Open Area:
Advantage: Metal
The most open metal belts (rod type) have more open area than the most open plastic belts.
Sanitation:
Advantage: Metal
Due to their construction, the more open metal belts (rod type) are easier to clean than the most open plastic belts.
Product Release:
Advantage: Plastic
The contact surface of plastic belts offers a more nonstick surface than metal belts.
Styles Of Belts Offered:
Advantage: Metal
Metal belts have more styles to choose from and more manufacturers.
Spiral Framework:
Advantage: Metal
Metal belts would generally be considered less complicated in frame construction due to the belt support system used. A typical 36" wide metal belt takes two supports for this width, while it takes 3 to properly support a plastic belt (due to lateral belt deflection). This can be avoided with plastic by putting metal connector rods periodically into the belt (to obtain lateral stiffness). On the flip side, it could be proven that metal belts typically run on horizontal and vertical plastic wear strips. A plastic belt could only be run on a metal structure, eliminating wear strips altogether. Construction could then be more accessible with plastic.
Belt Speeds:
Advantage: Plastic
Plastic belting has proven to be a better alternative when the application calls for higher belt speeds, as metal belts have typically been used only in applications where these speeds do not exceed 150 FPM.
Lubrication:
Advantage: Plastic
With plastic belts, you do not lubricate at all. Lubrication is required in specific applications of metal belts to reduce friction.
Belt Life:
Advantage: Metal / Plastic
Since plastic belts have a lower friction factor and typically run at fewer belt tensions than metal, we expect plastic belts to outlast metal on a given suitable application. However, plastic belts on spirals are still relatively new (13 years compared to 33 years on metal).
Heat:
Advantage: Metal
Metal belts are the best choice for now (over 220 degrees F) due to both plastic material compositions and the costs associated with high-temperature materials.
Radius Weight:
Advantage: Plastic
In all applications, available strength factors and expected belt tensions for both metal and plastic are related to the “radius weight factor,” which is the weight of the product and the belt multiplied by its radius. A lighter belt allows for more capabilities.
Airflow:
Advantage: Metal
Most open metal belts have better vertical airflow than most open plastic belts, but most airflow patterns used today are horizontal, so review your application to see if this will affect it in any way.
Thermal Conductivity:
Advantage: Metal
Metal belts have better thermal conductivity properties than plastic belts.
Flammability:
Advantage: Metal
Metal belts do not support a flame, while the standard plastic belts can.
Note: There are plastic belt materials that are self-extinguishing.
Drive Ability:
Advantage: Plastic
Plastic belts have a more significant surface area than metal belts, which enhances them for lower-tension systems.
Particulates:
Advantage: Plastic
In certain applications, metal belts can generate filings or metal particulates due to the connector rod and link interface. This is not an issue with plastic.
Repair Ability:
Advantage: Metal
Since plastic belts are modular in design, maintenance and repairs made in the field are more accessible and quicker than metal belts. No special tools, grinding, or welding are necessary.
Cost:
Advantage: Metal
The least expensive metal belt is cheaper than the least costly plastic belt. Metal belts have an advantage overall because they are not petroleum-based.
Example:
Grid belt $ .55/in of width
Flex belt $ .91/in of width
Mesh overlay belt $ .90/in of width
Plastic belt $1.10 1.48/in of width
For actual pricing per application, please get a quote. The above are pure guesstimates.
The More You Know About Freezers
The More You Will Look To Advanced Equipment Inc. as Your Reliable Supplier