From Interest to Delivery – The Buying Step Process
When Buying an Advanced Food Plant Freezer System
Below is a brief overview of our client commitment.
Advanced Equipment works to provide services that are unmatched in the industry.
Step 1) Sales Customer inquiry Arrives
- Within one day, our sales associate contacts the customer through e-mail and telephone.
- Within one week, we follow up to confirm the customer's request on product specification and freezing requirement.
- We discuss items such as freezer engineering, specifications, enhancement options, drawings and price.
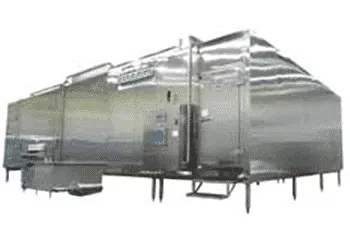
Step 2) We Prepare Accurate Drawings
- According to the customer's request, prepare an accurate layout drawing within one week.
- Approval from the customer is required for the freezer model number and design requirements.
- The project is discussed among the project engineer and sales for finalization on the freezer design.
- The project is assigned to individual project engineers, so there is clear communication between the client and our engineer.
- The project is passed to a team of draftsmen to create a construction drawing for manufacturing.
- All drawings are done with AutoCAD and 3-D modeling.
- Before production, all drawings are approved by a professional engineer.
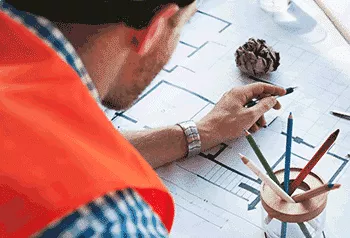
Step 3) Develop Plant Design Layout
- The project engineer will submit fully detailed freezer dimensions, layouts, and utility requirements for the customer's plant design and layout to the customer.
- The customer will provide feedback on their desired connection points for utilities.
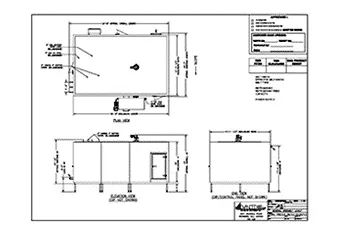
Step 4) Production Quality (Quality Control)
- The production manager assesses the information and checks for mistakes or ideas to improve the quality of production and the manufacturing cost.
- The project engineer constantly monitors and records manufacturing quality, such as the accuracy of the design welding, and checks for mistakes throughout the entire process.
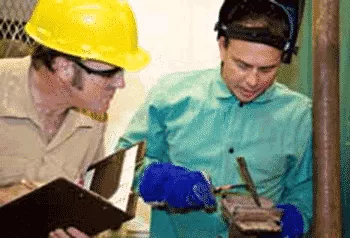
Step 5) Customer Visits Advanced Freezer Factory
- The project engineer informs the customer that the freezer is almost complete, and the customer can visit if necessary to see if any last-minute modifications are needed.
- The customer may visit and verify construction.
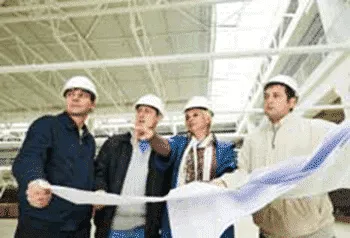
Step 6) Installation, Preparation And Testing
- Advanced Equipment will verify that the customer’s utilities are in place and ready for the freezer to be hooked up.
- Advanced Equipment will send the customer a list of materials needed during installation.
- Advanced Equipment will work with the customer’s schedule to determine the installation timeline.
- After completion, a licensed professional engineer completes the final testing and sign-off inspection of the freezer.
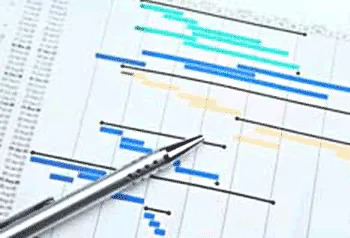
Step 7) Arrange Shipping & Prepare Unloading
- Tear down freezer modules at our facility for shipping wrapping.
- Arrange shipping trucking with insurance to the customer site.
- Inspect shipping protection and tight downs before shipping out.
- Inform customers of trucking and arrival schedules.
- Prepare the customer with unloading instructions and freezer moving-in-place arrangement.
- Schedule for an installer to assemble the freezer at the customer’s site.
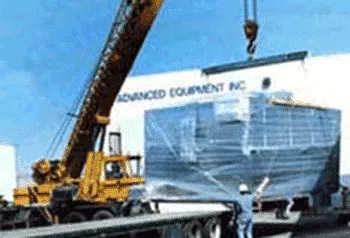
Step 8) Inspection, Assembly And Start Up
- Engineer starts up freezer with calibration on belt speed and CIP process.
- Hold instruction class with customers on freezer operation, safety, sanitation and maintenance.
- Customer signs off the freezer after installation and production.
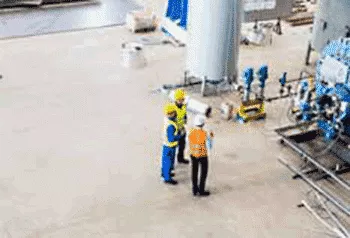
Step 9) Follow-Up
- Customer communications follow-up on freezer performance, calibration or problems.
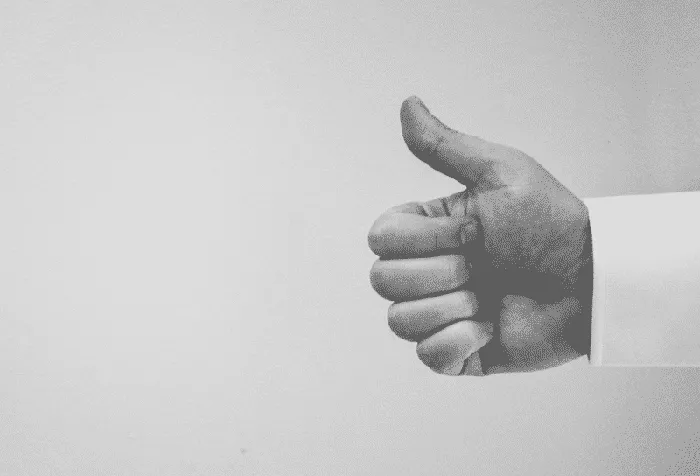